A análise de vibracións, a termografía, a análise de lubricantes, entre outras, son técnicas de mantemento preditivo que permiten atopar as causas de posibles avarías en previsión da avaría. Para a implantación do mantemento preditivo é fundamental levar a cabo un programa e unha organización que garantan o seguimento constante e rigoroso dos elementos que conforman a empresa.
Programa de mantemento preditivo
Os pasos nos que se basea o programa de mantemento preditivo pódense explicar do seguinte xeito. O programa de mantemento preditivo segue unha secuencia lóxica dende que se detecta un problema, se estuda, se atopa a súa causa e, finalmente, decídese a posibilidade de corrixilo no momento oportuno con máxima eficacia. Consta de tres pasos:
- Detección: Recoñecemento do problema.
- Análise: Localización da causa do problema.
- Corrección: atopar o momento e a forma de resolver o problema.
Como se dixo, a detección consiste en atopar un problema na maquinaria. Isto require un seguimento constante e rigoroso do nivel de vibración dunha máquina. O intervalo entre medicións depende de cada equipo e pode variar desde dous meses ata medición continua, dependendo do tipo e importancia do proceso. Os puntos elixidos para tomar vibracións son aqueles nos que se pode atopar algún defecto que afecte ao bo funcionamento da maquinaria serán lugares onde se aloxan rodamentos, ventiladores, engrenaxes ou xuntas entre eixes. Nos puntos a medir tomaranse valores de velocidade, aceleración ou desprazamento, en función da localización do punto e das características do
máquina.
O dispositivo utilizado será un colector de datos xunto cun programa informático que almacena os valores recollidos nas inspeccións rutineiras dos elementos da fábrica. A partir dun dato histórico dos puntos de cada máquina é posible detectar un problema cando a tendencia do valor aumenta ou cambia notablemente.
O seguinte paso é analizar o problema detectado unha vez atopado, identifícanse as súas posibles causas. Este estudo é complicado, depende en cada caso do punto onde aparece o defecto, da posición e do entorno da máquina. Non hai características que caractericen inequívocamente unha causa de exceso de vibración, pero a experiencia, o sentido común e o coñecemento de cada máquina son puntos esenciais.
Finalmente, o paso a seguir é a corrección da avaría detectada e analizada, polo que, unha vez detectado un problema e analizadas as súas causas, é necesario estudar as accións a realizar para solucionalo, ao mesmo tempo que se atopa a momento idóneo para a súa reparación, procurando que sexa o máis eficiente posible e que incida mínimamente no proceso produtivo, aproveitando unha parada ou unha situación na que a carga de traballo da máquina sexa menor que noutras.
Organización do programa de mantemento preditivo
A vixilancia estrita e constante das vibracións da máquina permite avisar previamente dunha avaría que pode forzar a súa parada súbita, co que isto pode implicar desde o punto de vista da produción. Ao mesmo tempo, este tipo de mantemento pode reducir custos en cambios de elementos programados e aínda poden seguir funcionando durante máis tempo. É polo tanto unha forma de mellorar a eficiencia do mantemento preventivo. Os seguintes nove pasos son importantes para organizar o mantemento preditivo:
- Recoñecemento de plantas
En primeiro lugar, antes de implantar o mantemento preditivo, é necesario decidir a necesidade e a eficacia nunha empresa. Esta decisión dependerá do tipo de máquinas, da cantidade e da súa importancia no proceso. - Selección de máquinas
Dentro dunha fábrica, realizarase un estudo de vibracións segundo un cronograma establecido daqueles equipos que forman parte do proceso produtivo de forma esencial, é dicir, aqueles cuxa avaría suporía perdas importantes dende o punto de vista da produción, por exemplo perdas económicas, dificultade e tempo de reinicio. Así mesmo, realizarase un seguimento constante da parte da maquinaria que polo seu tamaño ou valor económico ou produtivo sexa importante para a empresa. - Elixir técnicas óptimas para verificar
Forma de realizar a verificación, decidindo que, como, cando, onde se van realizar as medicións. - Implementación de predición
O programa de implantación preditiva debe conter:- Máquinas para estudar.
- Sistema de medida, recollida de datos e análise dos mesmos.
- Datos para comparar.
- Coñecemento do tipo de mantemento e dos medios para recoller datos.
- Establecemento e revisión de datos e límites de condicións aceptables
Para establecer un límite segundo valores que se poden chamar normais, é fundamental dispor dun dato histórico obtido
medicións repetidas. Un valor medio dos datos obtidos dará o nivel de vibración aceptable de cada un dos puntos.
medido. Os límites que determinan se un valor é aceptable estableceranse segundo estes datos históricos e experiencia.
Nun primeiro momento, cando non tes un conxunto de valores que che permitan estimar se unha vibración está dentro dos límites que
marque a súa normalidade, a aceptación dun valor farase a través das instrucións do fabricante e coas gráficas de
gravidade. - Medidas de referencia
Sempre haberá unha medida de referencia coa que se comparará cada unha das tomadas para comprobar se está dentro dos límites.
de aceptabilidade. - Recopilación, rexistro e análise de tendencias.
Aquí tentaremos detectar un posible defecto na máquina. - Análise do estado da máquina
Neste paso confirmarase se realmente existe un fallo e determinaranse as súas causas e a evolución que poden sufrir. - Correccións de erros.
Vibracións
Definición e características
Para comezar, pódese dar unha definición e características da vibración. A vibración é o movemento alternativo dunha máquina ou do seu elemento en calquera dirección no espazo desde a súa posición de equilibrio. Xeralmente, a causa da vibración reside en problemas mecánicos como: desequilibrio dos elementos xiratorios; desalineamento nos acoplamentos; engrenaxes desgastadas ou danadas; rodamentos deteriorados; forzas aerodinámicas ou hidráulicas e problemas eléctricos.
Estas causas, como se pode supoñer, son forzas que cambian de dirección ou de intensidade. Estas forzas débense ao movemento de rotación das pezas da máquina, aínda que cada un dos problemas se detecta estudando as características de vibración. As características máis importantes son: frecuencia, desprazamento, velocidade, aceleración, enerxía de pico.
A frecuencia é unha característica sinxela e significativa nesta análise. Defínese como o número de ciclos completos nun período de tempo. A unidade característica é cpm (ciclos por minuto). Existe unha importante relación entre a frecuencia e a velocidade angular dos elementos xiratorios. A correspondencia entre cpm e rpm (ciclos por minuto-revolucións por minuto) identificará o problema e a parte responsable da vibración. Esta relación débese a que as forzas cambian de dirección e amplitude segundo a velocidade de rotación. Os diferentes problemas son detectados por frecuencias iguais á velocidade de rotación ou múltiplos desta. Cada tipo de problema mostra unha frecuencia de vibración diferente.
A amplitude da vibración indica a importancia e gravidade do problema, esta característica dá unha idea do estado da máquina. Pódese medir a amplitude de desprazamento, velocidade ou aceleración. A velocidade de vibración ten en conta o desprazamento e a frecuencia, polo que é un indicador directo da gravidade da vibración. A severidade da vibración indícase con máis precisión medindo a velocidade, a aceleración ou o desprazamento segundo o rango de frecuencias entre o que se produce, polo que para frecuencias baixas, por debaixo de 600 cpm, tómanse medidas de desprazamento. No intervalo entre 600 e 60.000 cpm, mídese a velocidade, e para frecuencias altas, superiores a 60.000 cpm, tómanse aceleracións.
A velocidade é outra característica importante na vibración, graficamente pódese ver na figura 1.
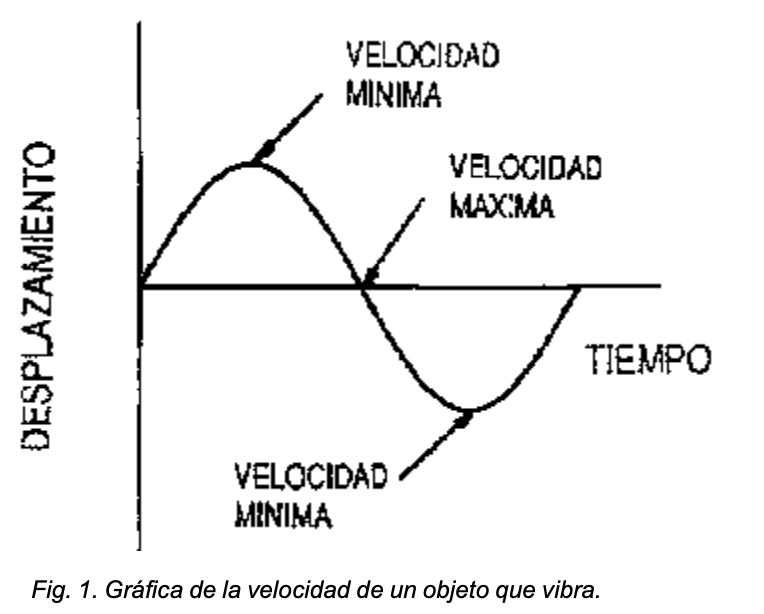
Mídese a velocidade máxima máis alta de todo o camiño que percorre o elemento cando vibra. A unidade é mm/s. Cambiar esta característica trae consigo un cambio na aceleración. A velocidade ten unha relación directa coa gravidade da vibración, por iso é o parámetro que sempre se mide. As vibracións que se producen entre 600 e 60.000 cpm analízanse tendo en conta o valor da velocidade.
A aceleración está relacionada coa forza que provoca a vibración, algunhas delas ocorren a altas frecuencias, aínda que a velocidade e o desprazamento son pequenos. Na figura 2 pódese ver a aceleración da vibración.

A enerxía de pico ou de impulso proporciona información importante ao analizar as vibracións. Este parámetro mide pulsos de enerxía de vibración de curta duración e, polo tanto, de alta frecuencia.
Poden ser impulsos debidos a: Defectos na superficie dos elementos de rodamentos ou engrenaxes. Fricción, impacto, contacto metal-metal en máquinas rotativas. Fugas de vapor ou aire a alta presión. Cavitación por turbulencia nos fluídos.
Sen este parámetro é moi difícil detectar engrenaxes ou rodamentos defectuosos. Con esta medida atópanse rapidamente as vibracións de alta frecuencia provocadas por estes defectos. O valor da enerxía de pico é basicamente unha medida da aceleración, pero a súa unidade é g-SE.
Gravidade da vibración
Un punto importante cando se fala de vibracións é coñecer a gravidade da vibración, indica a gravidade que pode ter un defecto. A amplitude da vibración expresa a gravidade do problema, pero é difícil establecer valores de limiar de vibración que detecten un fallo.
O obxectivo da análise de vibracións é atopar un aviso con tempo suficiente para poder analizar as causas e como solucionar o problema, provocando a mínima parada posible da máquina.
Unha vez obtidos os datos históricos de cada elemento das máquinas que se estudan, o valor medio reflicte a normalidade do seu funcionamento. As desviacións continuas ou excesivas indicarán unha posible avaría que se identificará posteriormente, tendo en conta a frecuencia na que se producen as vibracións máis altas.
Cando non hai datos históricos para unha máquina, pódese analizar a gravidade da vibración tendo en conta os seguintes gráficos (figs. 3 e 4):

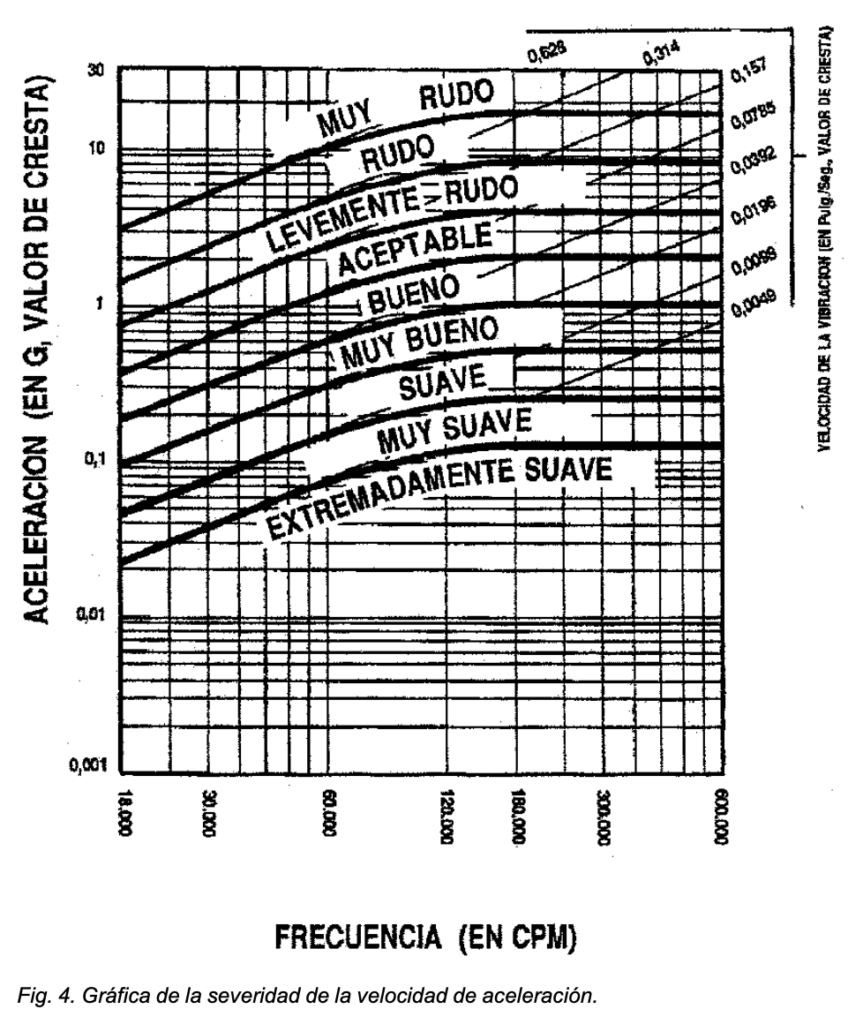
Análise
A esencia do estudo das vibracións é realizar a súa análise. A análise de datos consta de dúas etapas: adquisición e interpretación dos datos obtidos mediante a medición da vibración da máquina. O obxectivo a acadar é determinar as condicións mecánicas dos equipos e detectar posibles fallos mecánicos ou funcionais específicos.
A adquisición de datos é o primeiro e principal paso a dar para facer unha análise de vibracións. Os datos a tomar, desprazamento, velocidade ou aceleración dependerán da velocidade da máquina, segundo a súa relación de frecuencia equivalente (rpm=cpm). Así, para baixas revolucións (cpm baixas), tomaranse datos de desprazamento. Para velocidades que estean dentro do rango de 600 e 60.000 rpm, mediranse as velocidades. E para os que sexan de orde superior, os datos a tomar serán as aceleracións (fig. 5).
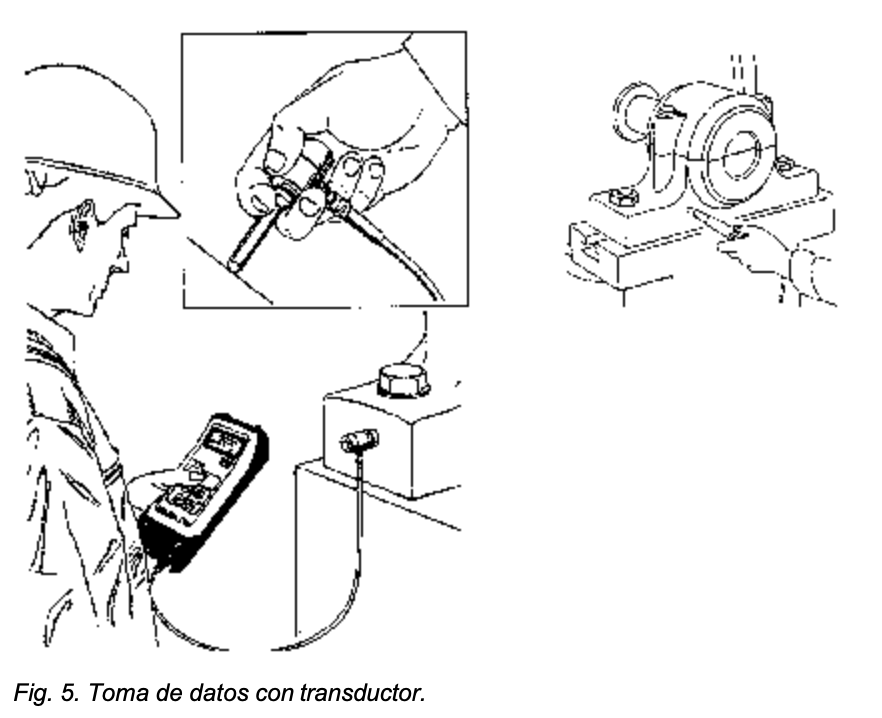
Pasos a seguir na adquisición de datos:
- Determinación das características de deseño e funcionamento da máquina, tales como: velocidade de rotación da máquina, tipo de rodamento, engrenaxe e condicións do entorno no que se sitúa como tipo de apoio, acoplamentos, ruído, etc. Tamén haberá que ter en conta as condicións de funcionamento como velocidade e cargas entre outras que afectarán normalmente ás medicións de vibración.
- Determinación do propósito da vibración que pode incluír:
Medidas rutineiras para detectar un posible fallo nun momento determinado e determinar as causas que o provocan. Medidas para crear un historial de datos e con ela obter un valor base, sobre o que estará o valor de vibración que debería ter a máquina cando as súas condicións de traballo sexan normais. Tomando datos antes e despois dunha reparación, a medición antes revelará o problema, o elemento defectuoso e así a súa reparación será máis eficaz. Despois da reparación, adoptaranse medidas que indiquen a evolución do elemento substituído ou a corrección do defecto existente. - Selección de parámetros de medida: desprazamento, velocidade, aceleración, enerxía de pico. Eles determinarán o transdutor a utilizar.
- Determinación da posición e dirección das medidas cos transdutores, a vibración tomarase xeralmente nos rodamentos da máquina ou nos puntos onde o fallo é máis probable por acoplamento, equilibrio, puntos onde se transmiten as forzas vibratorias. As tres direccións principais dunha medida son horizontal, vertical e axial. As direccións radiais son horizontais e verticais, e tómanse co eixe do transdutor a 90º con respecto ao eixe de rotación, como se ve na figura 6.
- Selección do instrumento de medida e dos transdutores.
- Determinación do tipo específico de datos necesarios para a interpretación das medicións realizadas. Isto aforrará tempo á hora de realizar as medicións e obterase delas máis información útil na análise. Os datos obtidos poden ser: valores de magnitude total, espectro amplitude-frecuencia que indica o tipo de problema existente, amplitude-tempo para vibracións transitorias rápidas ou vibracións moi lentas, enerxía de pico en rodamentos, engrenaxes e problemas de cavitación (fig. 7).
- Recollida de datos. Paso esencial na análise, que require atención e fiabilidade das medidas adoptadas. Ao adquirir datos é importante ter en conta:
- As secuencias de medición, tomando datos correctos o máis rápido posible, evitan a perda de tempo.
- O lugar de recollida de datos será sempre o mesmo, co transdutor firmemente conectado, para a veracidade dos datos.
- Vixilancia da máquina, é dicir, mantendo contacto cos operarios que traballan con ela e os operarios de mantemento, serán as persoas que coñezan de preto a máquina.
- Controla o ambiente externo da máquina, o aspecto, o ruído, etc.
- Abordar tendencias inesperadas. Estea preparado para tomar máis datos, medicións cando poida haber sinais dalgúns
problema. - Mantén só datos consistentes, tomados con precisión.
- Comparar con máquinas similares e da mesma forma de traballar.
Polo tanto, pódese dicir que a recollida de datos é un paso esencial para unha boa análise de vibracións. Para unha boa interpretación dos datos é necesario contar con datos fiables que se tomaron de forma metódica e precisa. Deste xeito, pódese facer un diagnóstico dun problema coa maior precisión posible.
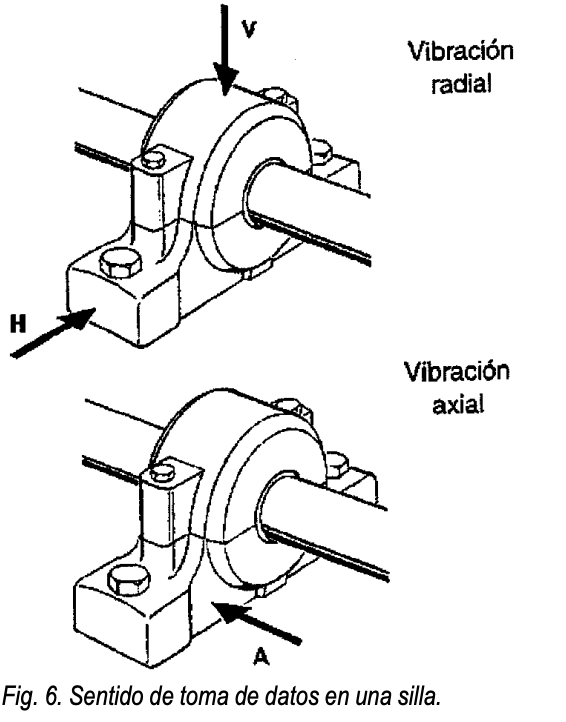
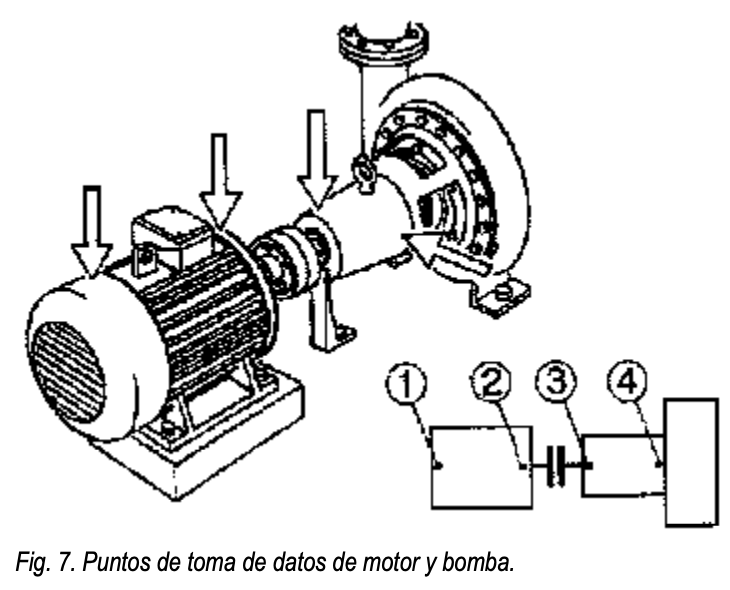
Identificación das causas das vibracións. Interpretación de datos
Unha vez obtidos de forma metódica e precisa os datos de vibración dunha máquina onde se detectou un problema, cómpre identificar cal foi a súa causa e buscar así o xeito e o tempo de reparación máis eficientes, é dicir, aquel que elimina o fallo e o seu custo económico é o mínimo posible.
Pódese localizar un defecto comparando as amplitudes das vibracións tomadas. Normalmente unha máquina que funciona correctamente ten valores que adoitan seguir unha liña cunha tendencia lixeiramente alcista ou constante. Cando nalgún momento os valores aumentan ou a tendencia sobe dun xeito inesperado, pódese pensar na presenza dun problema.
En xeral, os valores de amplitude que se comparan son os de velocidade Unha vez observado que esta aumentou de forma inesperada, é importante comparar os valores da enerxía do pulso (g). indicará a gravidade do problema. Así, pódese detectar un fallo atopando unha tendencia de velocidade ascendente inesperada e valores altos do parámetro g. Tamén é posible que se hai un problema haxa valores de enerxía de pico elevados e que de súpeto diminúan e aumenten gradualmente, isto pode levar a un fallo total, onde a máquina deixa de funcionar. Os valores de enerxía de pico elevados poden ser indicadores na maioría dos casos de problemas de rodamentos e acoplamentos e nos casos máis raros de problemas hidráulicos.
Xeralmente, a máxima amplitude de vibración prodúcese nos puntos onde se atopa o problema, aínda que moitas veces a vibración transmítese a outros puntos da máquina aínda que non se atope alí o problema. A análise dos gráficos pode indicar o tipo de defecto que existe, pero moi poucas veces aparecen problemas únicos e, polo tanto, espectros onde se reflicte claramente un defecto. A experiencia e o coñecemento da máquina son dous factores fundamentais á hora de identificar a causa que produce unha vibración importante.
É fundamental, unha vez corrixido o problema, seguir a evolución da reparación, deste xeito saberase se realmente existía o defecto, se estaba situado no punto de máxima vibración e, o que é máis importante, seguir o evolución tras a reparación e asegurarse de que o problema desapareceu.
O estudo dos datos de vibración e os seus espectros é a base para atopar as causas e como corrixir o defecto que indican. Só é importante prestar especial atención ás vibracións que se acompañan doutros efectos como ruídos, perdas de aceite ou calquera fallo, ou valores de amplitude excesivos en comparación con outros nun correcto funcionamento, a forma das vibracións analizaranse espectros que identificarán as causas dos problemas.
Os problemas mecánicos máis habituais nas máquinas que producen vibracións son o desequilibrio entre os eixes, a falta de aliñación dos acoplamentos, os defectos nos rodamentos e engrenaxes e os problemas eléctricos. A continuación podes ver como identificar estes problemas analizando os datos e os espectros de vibración.
Desequilibrio
Esta é unha das causas máis probables de vibración nas máquinas en case todos os elementos é fácil atopar un pico na gráfica de amplitude fronte a frecuencia, o que denota un pequeno desequilibrio. Como se pode observar no seguinte gráfico (fig. 8) hai un pico cunha frecuencia que coincide coa velocidade de rotación.
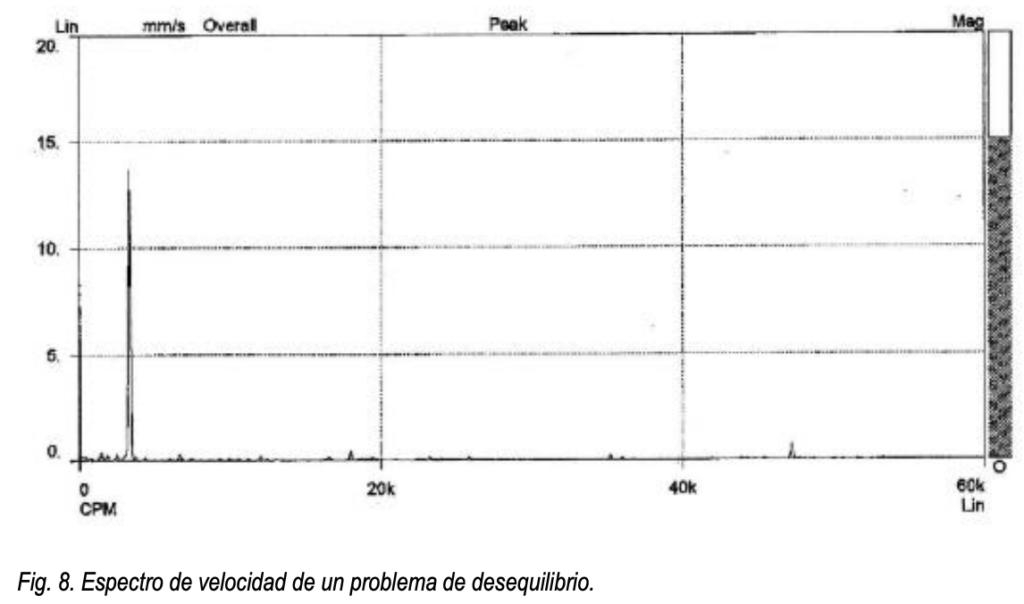
Para coñecer a cantidade de desequilibrio, debes atopar a amplitude da vibración a unha frecuencia igual a 1 x rpm. A amplitude é proporcional á cantidade de desequilibrio. Normalmente, a amplitude de vibración é maior na dirección radial (horizontal e vertical) nas máquinas con eixes horizontais, aínda que a forma da gráfica é a mesma nas tres direccións. Como se dixo antes, para analizar os datos de vibración, a experiencia e o coñecemento da máquina son tan importantes como os datos que se recollen dela. Cando aparece un pico cunha frecuencia igual a 1 x rpm. O desequilibrio non é a única causa posible, o desalineamento tamén pode producir picos nesta frecuencia. Cando aparecen vibracións a esta frecuencia, outras posibles causas son engrenaxes ou poleas excéntricas, falta de aliñación ou eixe retorcido se hai vibración axial elevada, correas en mal estado (se coincide coas súas revolucións), resonancias ou problemas eléctricos, nestes casos tamén. Desde o pico a unha frecuencia de 1 x rpm haberá vibracións noutras frecuencias.
Desalineación
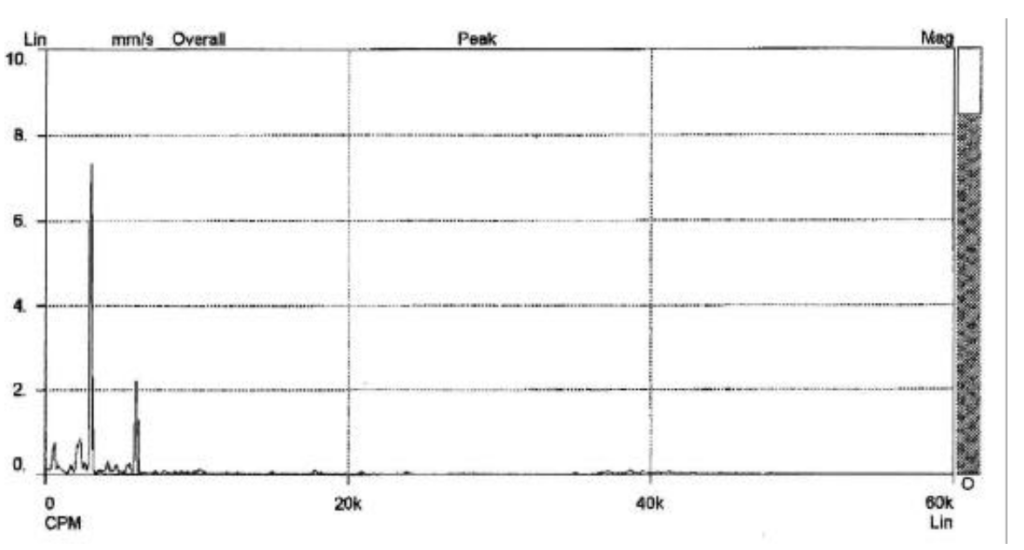
É un problema moi frecuente pola dificultade de aliñar dous eixes e os seus rodamentos para que non se xeren forzas que producen vibracións. O patrón de vibración dun eixe dobrado é similar ao da desalineación angular. Para recoñecer unha vibración por desalineación, pódense ver na gráfica picos a frecuencias iguais á velocidade de rotación do eixe, dúas ou tres veces esta velocidade nas situacións nas que este problema é grave. Un exemplo do espectro deste problema vese na figura 9, a forma do gráfico será similar nas tres direccións, só variando a amplitude. Como en todos os casos, a amplitude é proporcional á gravidade do defecto, aquí desalineación. Esta falla pode presentar altas vibracións na dirección axial e radial. Así, sempre que se produza unha vibración elevada en axial e radial, e se o axial é maior que a metade do radial, pode haber un problema de desalineación ou eixes torcidos. Na Figura 10 pódense ver os tres tipos básicos de desalineación, paralelo, angular e unha combinación de ambos. A falta de aliñación paralela, figura 11, produce principalmente vibracións na dirección radial cunha frecuencia igual ao dobre da velocidade de rotación do eixe.

A falta de aliñación angular, representada na Figura 12, provoca vibracións en dirección axial en ambos eixes a unha frecuencia igual a 1 x rpm.
As condicións de desalineación non sempre implican acoplamento. Un desalineamento entre o eixe e o seu cojinete, figura 13, é un exemplo común deste defecto e só se pode eliminar corrixindo a colocación do cojinete. Un casco mal aliñado co seu eixe, como se ve na figura 13, non crea vibracións importantes, salvo que tamén exista un problema de desequilibrio, este defecto sería o que provocaría unha falta de aliñación.
engrenaxes

Este defecto pódese observar atopando picos en frecuencias que coinciden con múltiplos enteiros da velocidade de rotación da engrenaxe que falla, ademais, haberá vibración de menor amplitude simétricamente na frecuencia da engrenaxe. Na Figura 14, pódense ver picos de valor significativo a frecuencias que son múltiplos da velocidade de rotación dun piñón. Simétricamente a estes picos, hai outros de moi pequeno valor e separados por unha distancia igual á velocidade de rotación.
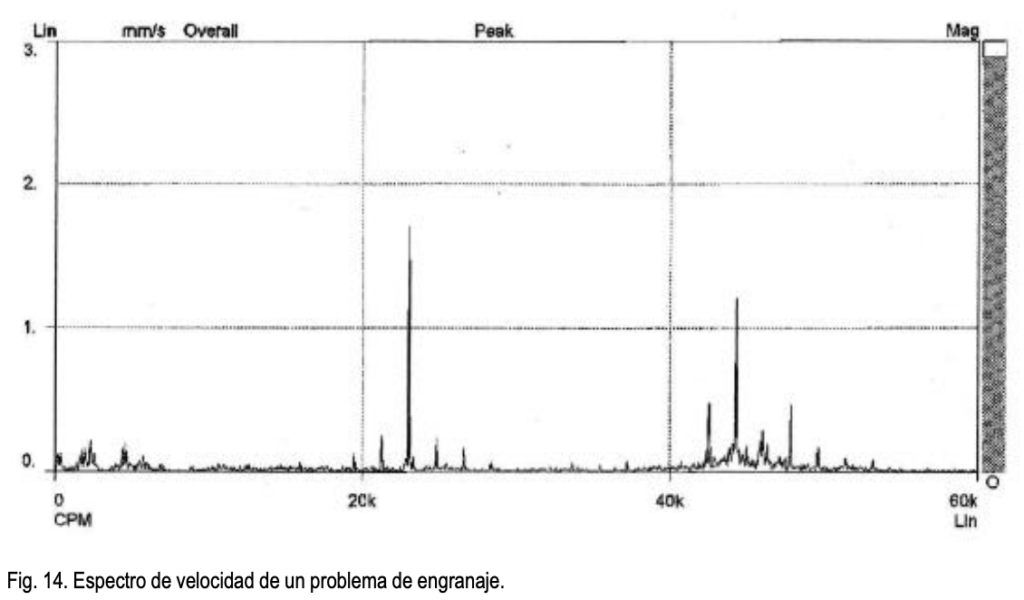
Os problemas de engrenaxe que provocan esta vibración son: desgaste excesivo dos dentes, imprecisión dos dentes, fallos de lubricación, elementos estraños entre os dentes. As vibracións causadas por defectos das engrenaxes pódense detectar en varios puntos das máquinas. Esta é unha característica que diferencia un gráfico causado por unha engrenaxe lixeiramente cargada e a vibración producida por un rodamento, xa que a gráfica de amplitude fronte á frecuencia pode resultar confusa cando a carga do piñón é baixa.
Tanto a falla de engrenaxes como a falla dos rodamentos tamén provocan a aparición de ruído.
problemas eléctricos
A vibración é creada por forzas desiguais que poden ser causadas pola forma interna do elemento. É difícil recoñecer graficamente este problema, xa que non ten características que simplemente indiquen que esta é a causa da vibración.
O espectro pode dar lugar a erros porque é semellante ao do desequilibrio, só aquí ao desconectar a corrente o problema desaparecerá. Os picos maiores detectaranse a distancias iguales a catro veces a velocidade de rotación se hai catro polos, distinguindo a vibración separada a unha frecuencia coincidente coa velocidade de rotación. A figura 15 mostra o espectro que dan este tipo de problemas.

Rodamentos
Os fallos nos elementos de rodamento dan vibracións a altas frecuencias non relacionadas coa velocidade de rotación e tamén en amplitude aleatoria. A continuación, nas figuras 16 e 17 pódense ver os espectros de velocidade e aceleración, respectivamente, dun rodamento de bolas defectuoso. É relativamente fácil recoñecer esta falla observando o gráfico amplitude-frecuencia, xa que se caracteriza por ter moitos picos xuntos a altas frecuencias e de amplitude variable que dependerán da gravidade do problema. A frecuencia á que se produce a amplitude máxima pode dar unha idea do elemento de rodamento defectuoso. Os defectos dos elementos rodantes, pistas de rodamento ou gaiola de retención xeran forzas que se transmiten á carcasa e á estrutura que os rodea.

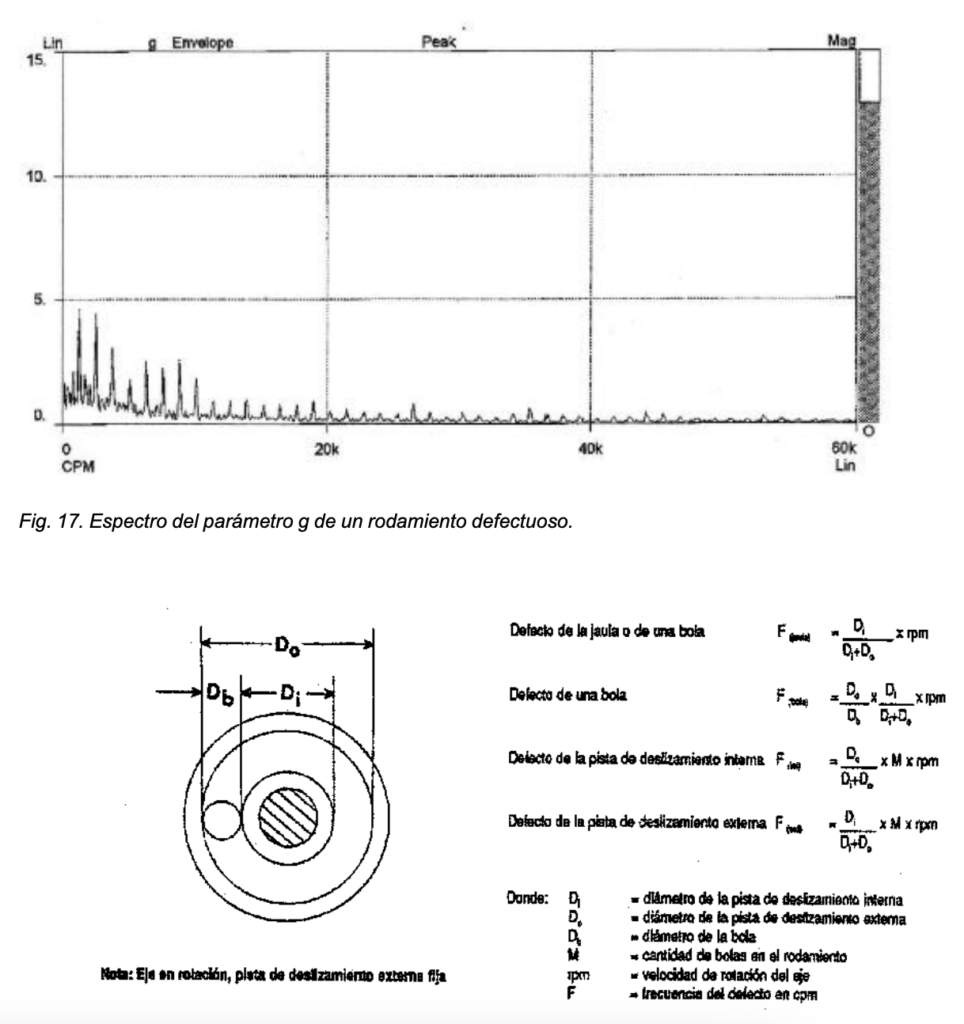
Para detectar que tipo de avaría existe, débese obter a frecuencia na que é maior a amplitude e comparala coas calculadas segundo as fórmulas da figura 18.
Cando esta é a causa da vibración é moi importante coñecer o valor da enerxía do pico, con este parámetro pódese intuir a gravidade do problema. O gráfico que representa a frecuencia g indica que a vibración do rodamento a alta frecuencia é inestable e xerada aleatoriamente.
Así, o estado da máquina identifícase segundo a seguinte táboa:
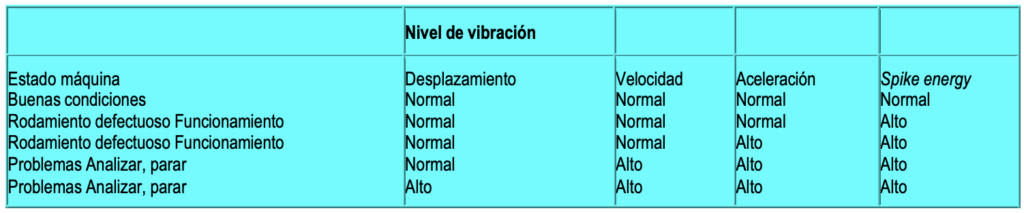
A falla dun rodamento detéctase só na medición realizada sobre el, é dicir, non se transmitirá ao resto dos puntos da máquina. Externamente, o rodamento defectuoso será perceptible debido ao ruído excesivo.
Os rodamentos son elementos importantes na máquina e cuxa avaría pode provocar problemas máis graves, polo que é necesario ter especial coidado con eles. Poden fallar por erros de montaxe, lubricación inadecuada, defectos internos de fabricación, corrente eléctrica, desalineacións, rodamentos non preparados para a carga que soporta. Estas son as causas máis comúns de fracaso.
Polo tanto, a análise de vibracións é unha técnica que, aínda que non é exacta, é capaz de atopar avarías nas máquinas, anticipándose á avaría. As vantaxes de realizar este tipo de mantemento son a desaparición de avarías bruscas nos equipos estudados, o coñecemento do estado da máquina en cada momento. Isto reduce os custos económicos por reparacións imprevistas, paradas no proceso de produción, cambios de elementos que aínda poden seguir funcionando, aumento da eficiencia e reducións dos custos dunha parada, ademais de todo isto, contribúe a mellorar o mantemento preventivo realizado no fábrica. Detrás de todo isto, as vantaxes que ofrece este estudo son sobre todo económicas,
seguridade contra avarías súbitas.